Our Services
We provide maintenance and inspection of marine safety equipment according to SOLAS regulations.
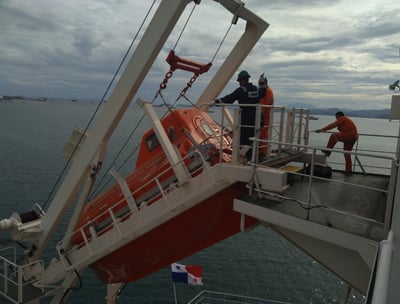
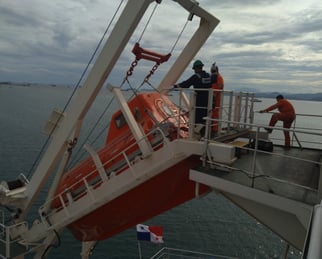
Lifeboat and rescue boat inspections meticulously examine the boats' hulls, engines, equipment, and overall condition, while launching appliances and release gear inspections focus on the davits, winches, wires, and release mechanisms to ensure safe and efficient deployment in emergencies. These comprehensive inspections, mandated by regulations like SOLAS, are performed regularly by qualified personnel to guarantee the reliable operation of these critical life-saving systems, safeguarding lives at sea.
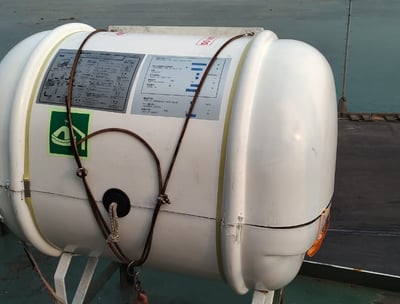
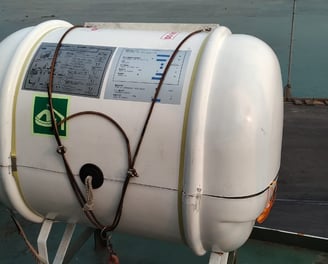
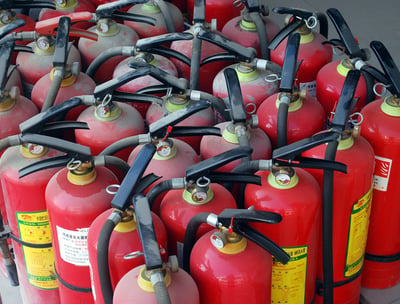
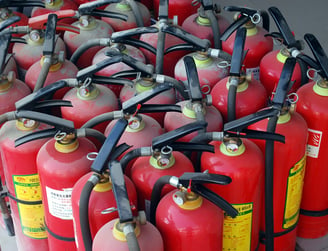
Inflatable liferaft and life saving appliances inspections are crucial for ensuring maritime safety, involving thorough checks of the liferaft's inflation system, contents, and container, as well as the functionality and condition of other life-saving equipment like life jackets, lifebuoys, and pyrotechnics. These inspections, conducted regularly by certified professionals and ship crews, guarantee the equipment's readiness and reliability in emergency situations, adhering to international regulations like SOLAS to protect lives at sea.
Fire extinguishing system and equipment inspections encompass a thorough examination of all fire suppression components, including extinguishers, hoses, hydrants, alarms, and sprinkler systems, to ensure they are readily accessible, fully functional, and properly charged or pressurized. These inspections, conducted regularly according to established schedules and regulations like NFPA or SOLAS, verify the operational readiness of these critical life safety systems, minimizing fire risks and protecting lives and property.
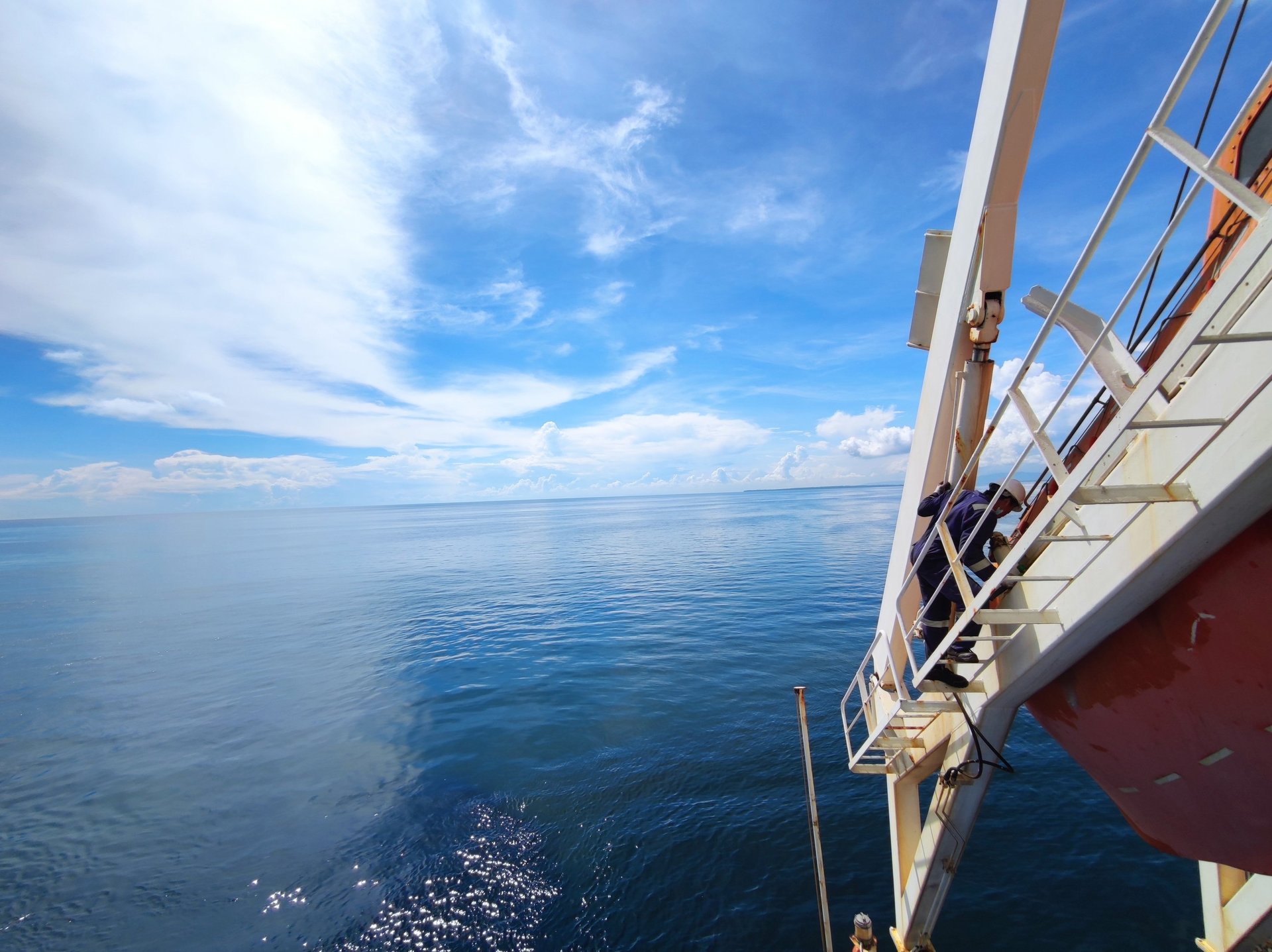
1. Lifeboat & Rescue Boat Inspection:
This inspection focuses on the physical condition and functionality of the boat itself. Key areas include:
Hull and Structure: Checking for damage, corrosion, or deterioration.
Engine and Propulsion: Ensuring the engine starts reliably and runs smoothly, checking fuel levels, and inspecting the propeller and steering mechanism.
Buoyancy and Stability: Inspecting buoyancy compartments and ensuring the boat's stability.
Equipment and Fittings: Verifying the presence and condition of essential equipment like oars, life jackets, first aid kits, signaling devices, and navigation equipment.
Electrical Systems: Checking batteries, lights, and other electrical components.
2. Launching Appliances Inspection:
This inspection focuses on the mechanisms used to launch the lifeboat or rescue boat. Key areas include:
Davit and Winch Systems: Inspecting davits for structural integrity, checking winch operation, wire ropes, and brakes.
Sheaves and Blocks: Ensuring smooth operation and checking for wear and tear.
Foundation and Securing Arrangements: Inspecting the foundation of the launching appliance and ensuring it is securely attached to the ship's structure.
Limit Switches and Safety Devices: Checking the functionality of limit switches and other safety devices to prevent accidents during launching.
3. Release Gear Inspection:
This inspection focuses on the mechanism that releases the lifeboat or rescue boat from the launching appliance. Key areas include:
On-Load Release Mechanism: Ensuring the mechanism releases the boat smoothly and reliably under load.
Off-Load Release Mechanism: Checking the functionality of the off-load release mechanism, used when the boat is not under load.
Interlocks and Safety Devices: Inspecting interlocks and safety devices to prevent accidental release.
Hydrostatic Release Unit (HRU): If fitted, inspecting the HRU for proper operation and expiry date.
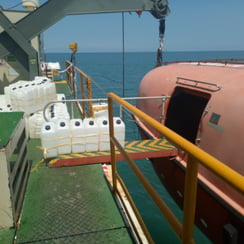
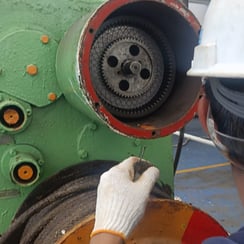
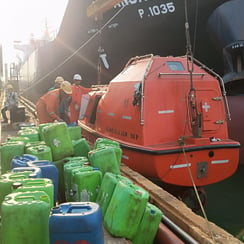
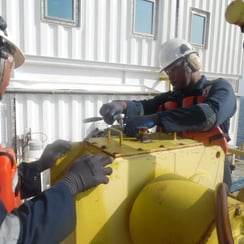
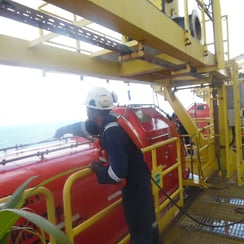
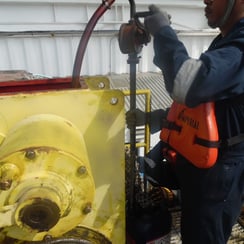
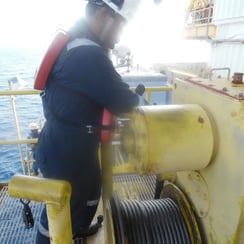
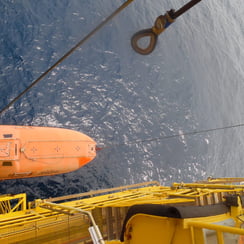
Regulations and Standards:
These inspections are typically carried out according to international regulations such as the International Convention for the Safety of Life at Sea (SOLAS) and the International1 Life-Saving Appliance (LSA) Code. These regulations specify the frequency and scope of inspections, as well as the requirements for maintenance and testing.
Frequency of Inspections:
Weekly and Monthly Inspections: These are typically carried out by the ship's crew and involve visual checks and basic functional tests.
Annual Inspections: These are more comprehensive and may involve testing of the launching appliances and release gear under load.
Overhaul and Operational Tests: These are typically carried out every five years and involve a thorough inspection and testing of all components.
Importance of Inspections:
Regular inspections and maintenance are crucial for ensuring the reliability of lifeboats and rescue boats in emergencies. Proper inspection ensures:
Operational Readiness: The boats and launching appliances are ready for immediate use in an emergency.
Safety of Crew and Passengers: Properly functioning life-saving appliances increase the chances of survival in maritime accidents.
Compliance with Regulations: Regular inspections ensure compliance with international regulations and prevent potential penalties.
The inspection of lifeboats, rescue boats, launching appliances, and release gear is a critical aspect of maritime safety. By adhering to regulations and conducting thorough inspections, we can ensure the operational readiness of these vital life-saving appliances and protect lives at sea.
We provide maintenance and inspection of lifeboats & Rescue Boats, Launching Appliances & Release Gear to ensure optimal seaworthiness and meet applicable international standards.
Lifeboats and rescue boats are critical life-saving appliances on board a ship, used in emergencies for safe evacuation. Regular inspections and maintenance are crucial to ensure their operational readiness. These inspections cover various aspects, including the boat itself, its launching appliances, and the release gear.
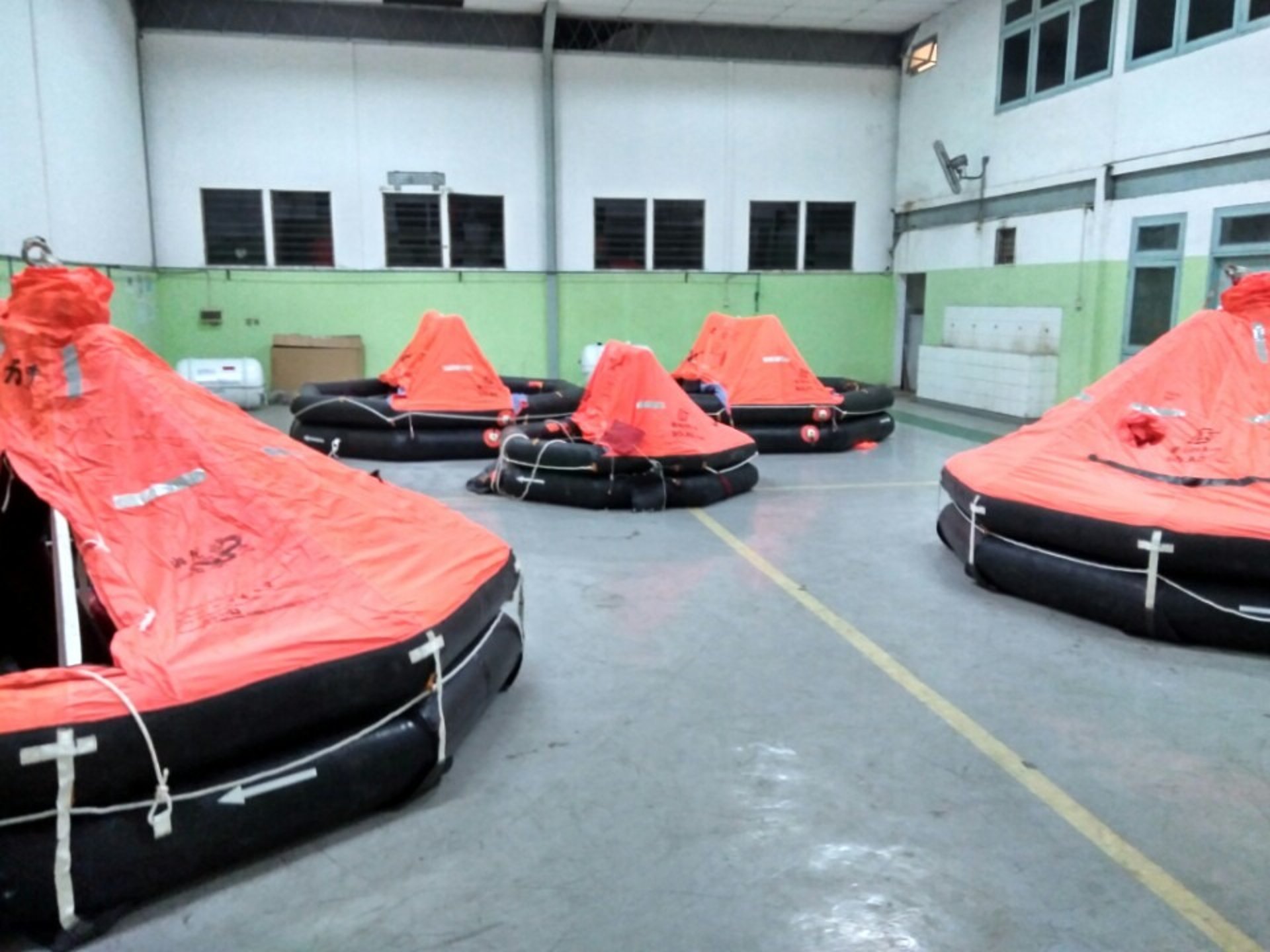
The inspection of liferafts and other Life Saving Appliances (LSA) is a comprehensive process, encompassing visual checks, operational tests, and thorough servicing. Visual inspections meticulously examine the equipment for any signs of physical damage, wear and tear, corrosion, or deterioration. This includes scrutinizing the liferaft container for rust or dents, checking life jacket fabric for tears, and ensuring reflective tape is intact and functional. Operational tests then verify the functionality of critical systems, such as the inflation mechanisms of liferafts, the lights and whistles on life jackets, and the release mechanisms of launching appliances. Servicing, typically conducted at approved service stations for liferafts, involves more in-depth procedures like pressure testing, valve checks, and replacement of expired components such as batteries, pyrotechnics, and food rations.
Adherence to established regulations is paramount in LSA inspection. International regulations, most notably the International Convention for the Safety of Life at Sea (SOLAS), along with relevant national regulations, dictate the frequency and scope of these vital inspections. Liferafts, for instance, generally require annual servicing at certified facilities, while other LSA like life jackets and lifebuoys undergo regular visual inspections by crew members and more detailed inspections at specified intervals. Maintaining meticulous records of all inspections, including dates, findings, and any maintenance performed, is crucial for demonstrating compliance and ensuring accountability.
These records should be readily accessible for review by port state control officers or other authorized personnel. The effectiveness of LSA hinges on the proper functioning of even the smallest components. During inspections, attention to detail is crucial. For liferafts, this includes verifying the hydrostatic release unit's (HRU) expiry date, checking the condition of the inflation cylinder and valves, and ensuring the contents of the emergency pack are complete, undamaged, and within their expiry dates. For life jackets, inspectors check the buoyancy material for leaks or damage, test the lights and whistles for proper operation, and thoroughly inspect the straps and buckles for secure fastening. These seemingly minor details can have a significant impact on the equipment's performance in a real emergency situation. Finally, effective LSA inspection requires trained and competent personnel. Inspectors must possess a thorough understanding of the relevant regulations, inspection procedures, and the specific characteristics of different types of LSA. This expertise enables them to accurately identify potential defects, conduct precise assessments, and perform necessary maintenance or repairs to the required standards. Regular training and certification programs are therefore essential for ensuring that inspectors maintain their proficiency and stay abreast of any updates in regulations, best practices, or evolving technology.
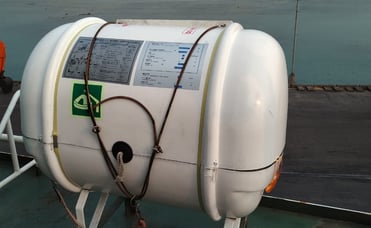
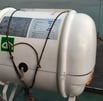
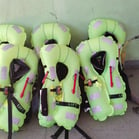
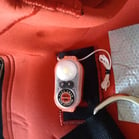
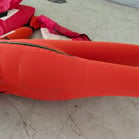
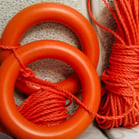
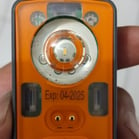
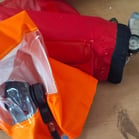
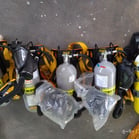
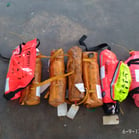
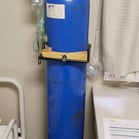
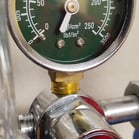
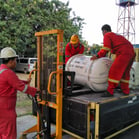
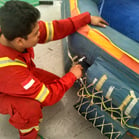
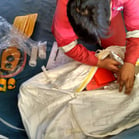
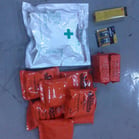
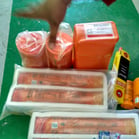
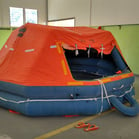
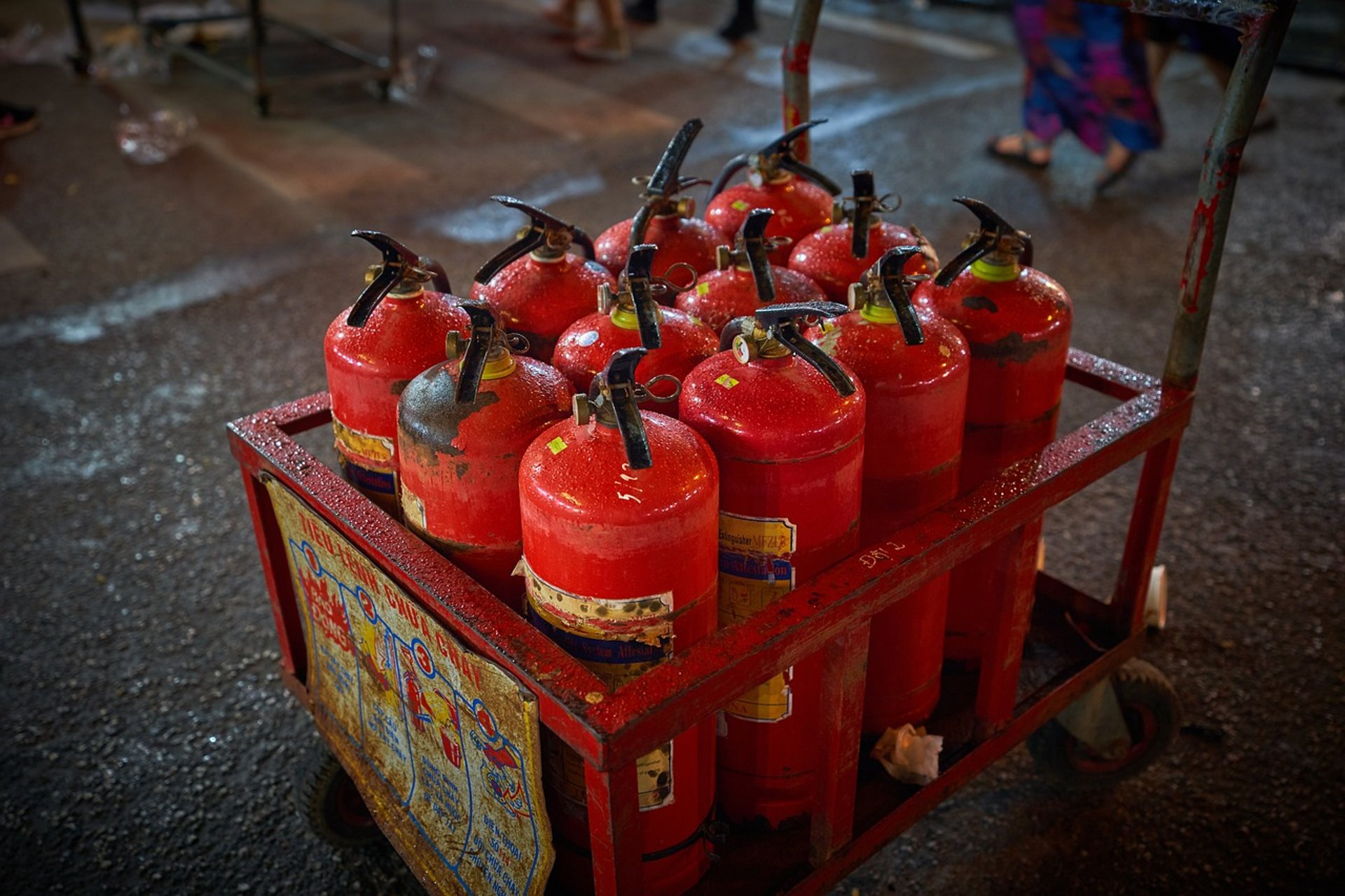
The inspection of fire extinguishing systems and equipment encompasses a range of procedures designed to ensure their readiness and reliability in fire emergencies. These procedures include regular visual inspections, functional testing, and periodic maintenance. Visual inspections focus on identifying any signs of damage, corrosion, leaks, or obstructions. This involves checking pressure gauges on extinguishers, inspecting hoses and nozzles for cracks or blockages, and ensuring that equipment is properly mounted and accessible. Functional testing verifies the operability of the equipment, such as discharging extinguishers (in a controlled manner and with appropriate recharge), testing the operation of alarms and detection systems, and confirming the proper functioning of valves and controls in fixed suppression systems.
The inspection of fire extinguishing systems and equipment encompasses a range of procedures designed to ensure their readiness and reliability in fire emergencies. These procedures include regular visual inspections, functional testing, and periodic maintenance. Visual inspections focus on identifying any signs of damage, corrosion, leaks, or obstructions. This involves checking pressure gauges on extinguishers, inspecting hoses and nozzles for cracks or blockages, and ensuring that equipment is properly mounted and accessible. Functional testing verifies the operability of the equipment, such as discharging extinguishers (in a controlled manner and with appropriate recharge), testing the operation of alarms and detection systems, and confirming the proper functioning of valves and controls in fixed suppression systems.
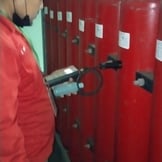
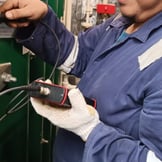
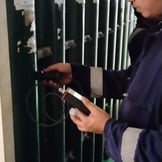
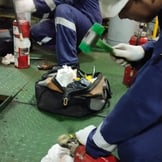
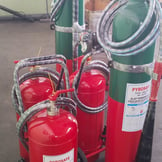
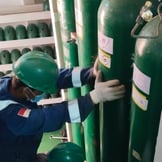
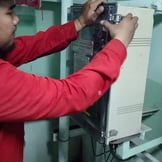
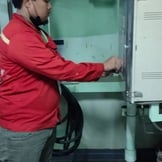
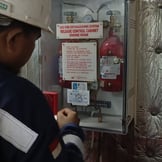
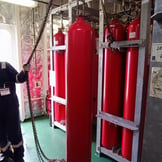
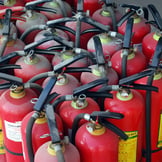
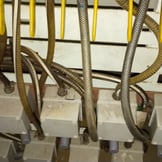
OUR CONTACT
© 2025. All rights reserved.
ADDRESS
Jl. Walang Baru No. 9, North Jakarta 14260
DKI Jakarta, Indonesia
+6221 43932388 (Office)
+6281 1874203 (Marketing)
+6281 212631073 (Admin)
info@semangat-semesta.com